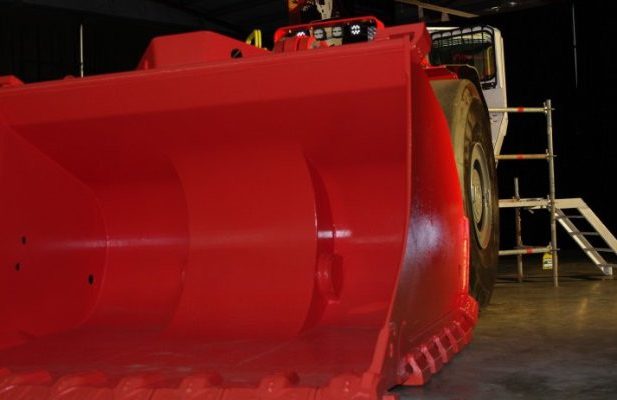
Sandvik has showed off its latest truck, the TH663i, and given an introduction to its next series of loaders with the TH517i.
The 17t loader is off to do trials in a Western Australian mine with the aim of it putting in about 2,000 hours.
It is not quite ready for commercial release just yet, but when it is Australia will get it ahead of some other countries. The machine is expected to be released to the Australian market in the June quarter next year and have its global launch in about September 2018.
That global launch will include the larger 621 loader as well.
One of the interesting things about the loader is that it pays homage, albeit subtly, to the old Toro name that miners knew the orange trucks and loaders by. On the back of the loader is the outline of a bull across the grille. When the brakes are applied, the bull gets red eyes.
When it came to considering its next round of equipment, Sandvik had to decide whether to junk the old design and start from scratch or improve what it had. After talking to customers it was decided that the improvement option was best.
In the case of the loader, some of those changes included creating more headroom and legroom in the cab and putting in a larger fuel tank. The 750L tank fitted to the machine is thought to be good for about 17 hours of operation.
One particularly clever addition is the mechanical retrieval hook on the back – in case the loader gets trapped in the muck pile. As force is applied to the retrieval hook it pulls out from the rear of the loader and that action releases the loader’s brakes.
The TH663i
On the truck front, Sandvik has launched the TH663i, a 63t articulated underground haul truck. The one Sandvik put on show in Perth last week had been fitted out for autonomous operation and will be used by Barminco.
Sandvik claims that the latest version of the 663i is up to 30% more productive than its predecessor.
One of the biggest changes to the truck is the addition of a 40m3 box to ensure that operations with low specific gravity material – such as gold mines – can get 63t in the truck. Those going with the 40m3 box get a wider rear axle, which brings the machine an extra 15% stability.
Sandvik has also upgraded both the hardware and software in the Allison transmission. The trainer’s seat has been fitted with an ‘optimised’ cushion and the rubber mat on the floor near the pedals has been replaced with an aluminium scuff plate to increase its longevity.
Sandvik has even added two cupholders to the cab and there is a ‘cold box’ behind the trainer’s seat that can help keep the operator’s drinks chilled.
The haulers are also set up for automation. Sandvik line manager underground trucks Mark Ryan said that Sandvik’s experience was that owners could get up to a 50% reduction in operational cost when running the machines autonomously. Sandvik has been working with part-time and full-time autonomous approaches.
In the full-time approach, a haul route is quarantined off from other vehicles and the trucks simply report to load points, get loaded, tram to the dump and return for loading.
One such example is Petra Diamonds’ Finsch mine in South Africa.
The part-time approach involves using the decline when the workings have been cleared of personnel for blasting.
Ryan said that Sandvik trialled the part-time approach at Agnico Eagle’s Kittilä gold mine in Finland. Kittilä also had an automated 517 loader.
During the two hour window on each shift when blasting was conducted, the automated loader and autonomous truck were able to keep working.
Ryan said the mine was getting an extra four loads per day and it gave Sandvik a chance to prove its blast clearance approach was a viable option.
Comments (0)